Future breakthroughs in fuel cell
technology will forever change our concept of the
automobile, transforming the way vehicles are designed,
manufactured and serviced. Fuel cells have the potential to
revolutionize every facet of our lives, powering not only
our mode of transportation, but our homes, schools, work and
entertainment as well. Widespread use of fuel cells may hold
the answers to some of our most significant energy shortage
challenges for the future and could mark a historical
turning point, reducing dependence on fossil fuels,
improving the environment and creating a whole new
hydrogen-driven economy. Our mission is to accelerate the
development and commercialization of fuel cells for
stationary, mobile, and portable applications by improving
the fuel cell performance, reliability, and durability while
reducing the cost of fuel cell components and systems
through innovations in materials, design and manufacturing
processes; and technological leadership in R&D, testing and
evaluation.
Objectives
-
Research and development of fuel cells.
-
New
designs for portable, mobile and stationary
applications.
-
Advanced modeling and design analysis tools.
-
Materials and component performance, reliability,
durability.
-
Manufacturing processes and production economics.
-
Fuel
processing, hydrogen production and storage, and related
technology.
-
Continuing education in fuel cell technology.
-
Interface between university and industry.
Research
1. Hygro-Thermal Stresses and Deformation Distribution in Tubular-Shaped Ambient
Air-Breathing PEM Micro Fuel Cell |
This
research investigates the displacement, deformation, and
stresses inside novel micro tubular design ambient air-breathing
proton exchange membrane fuel cell. An operating air-breathing
PEM fuel cell has varying local conditions of temperature,
humidity. As a result of in the changes in temperature and
moisture, the membrane, GDL and bipolar plates will all
experience expansion and contraction. Because of the different
thermal expansion and swelling coefficients between these
materials, hygro-thermal stresses are introduced into the unit
cell during operation. In addition, the non-uniform current and
reactant flow distributions in the cell result in non-uniform
temperature and moisture content of the cell which could in
turn, potentially causing localized increases in the stress
magnitudes, and this leads to mechanical damage, which can
appear as through-the-thickness flaws or pinholes in the
membrane, or delaminating between the polymer membrane and gas
diffusion layers. Therefore, in order to acquire a complete
understanding of these damage mechanisms in the membranes and
gas diffusion layers, mechanical response under steady-state
hygro-thermal stresses have been studied under real cell
operation conditions.
[Full Text (PDF)] |
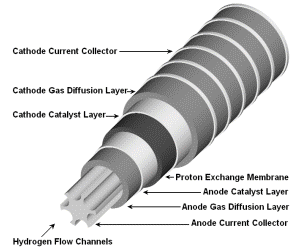 |
2.
Optimizes PEM Fuel Cell Durability |
Damage
mechanisms in a proton exchange membrane (PEM) fuel cell are
accelerated by mechanical stresses arising during fuel cell
assembly (bolt assembling), and the stresses arise during fuel
cell running, because it consists of the materials with
different thermal expansion and swelling coefficients.
Therefore, in order to acquire a complete understanding of the
damage mechanisms in the membrane and gas diffusion layers,
mechanical response under steady-state hygro-thermal stresses
should be studied under real cell operating conditions and in
real cell geometry (three-dimensional). In this work, the
mechanical behaviour of the membrane, catalyst layers, and gas
diffusion layers during the operation of a unit cell has been
studied and investigated. The results show that the non-uniform
distribution of stresses, caused by the temperature gradient in
the cell, induces localized bending stresses, which can
contribute to delaminating between the membrane and the gas
diffusion layers. These results may explain the occurrence of
cracks and pinholes in the membrane during regular cell
operation. Detailed analyses of the fuel cell durability under
various operating conditions (operating, design, and material
parameters) have been conducted and examined. The analysis
helped identifying critical parameters and shed insight into the
physical mechanisms leading to a fuel cell durability under
various operating conditions. Optimization study of a PEM fuel
cell durability has been performed. To achieve long cell life,
the results show that the cell must be operate at lower cell
operating temperature, higher cell operating pressure, higher
stoichiometric flow ratio, and must have higher GDL porosity,
higher GDL thermal conductivity, higher membrane thermal
conductivity, narrower gases channels, thicker gas diffusion
layers, and thinner membrane. In these optimum conditions, the
maximum deformation (displacement) is reduced by about 50% than
the base case operating conditions.
[Full Text (PDF)] |
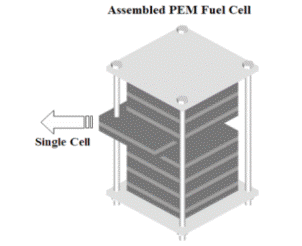 |
3.
Novel Design of a Compacted Micro-Structured Air-Breathing PEM Fuel Cell as a Power Source for Mobile Phones |
The presence
of microelectromechanical system (MEMS) technology makes it
possible to manufacture the miniaturized fuel cell systems for
application in portable electronic devices. The majority of
research on micro-scale fuel cells is aimed at micro-power
applications. There are many new miniaturized applications which
can only be realized if a higher energy density power source is
available compared to button cells and other small batteries. In
small-scale applications, the fuel cell should be exceptionally
small and have highest energy density. One way to achieve these
requirements is to reduce the thickness of the cell
(compacted-design) for increasing the volumetric power density
of a fuel cell power supply.
A novel, simple to construct, air-breathing micro-structured PEM
fuel cell which work in still or slowly moving air has been
developed. The novel geometry enables optimum air access to the
cathode without the need for pumps, fans or similar devices. In
addition, the new design can achieve much higher active area to
volume ratios, and hence higher volumetric power densities.
[Full Text (PDF)] |
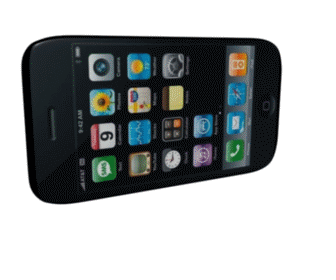 |
4.
Mechanical Behaviour of PEM Fuel Cell Catalyst Layers During
Regular Cell Operation |
Damage
mechanisms in a proton exchange membrane fuel cell are
accelerated by mechanical stresses arising during fuel cell
assembly (bolt assembling), and the stresses arise during fuel
cell running, because it consists of the materials with
different thermal expansion and swelling coefficients.
Therefore, in order to acquire a complete understanding of the
mechanical behaviour of the catalyst layers during regular cell
operation, mechanical response under steady-state hygro-thermal
stresses should be studied under real cell operating conditions
and in real cell geometry (three-dimensional). In this work,
full three-dimensional, non-isothermal computational fluid
dynamics model of a PEM fuel cell has been developed to
investigate the behaviour of the cathode and anode catalyst
layers during the cell operation. A unique feature of the
present model is to incorporate the effect of hygro and thermal
stresses into actual three-dimensional fuel cell model. In
addition, the temperature and humidity dependent material
properties are utilize in the simulation for the membrane. The
model is shown to be able to understand the many interacting,
complex electrochemical, transport phenomena, and deformation
that have limited experimental data.
[Full Text (PDF)] |
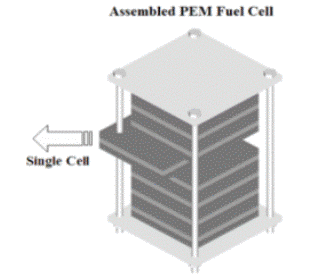 |
5.
Effect of Ambient Conditions on the Hygro-Thermal Stresses
Distribution in a Planar Ambient Air-Breathing PEM Fuel Cell |
The need for
improved lifetime of air-breathing proton exchange membrane (PEM)
fuel cells for portable applications necessitates that the
failure mechanisms be clearly understood and life prediction
models be developed, so that new designs can be introduced to
improve long-term performance. An operating air-breathing PEM
fuel cell has varying local conditions of temperature and
humidity. As a result of in the changes in temperature and
moisture, the membrane, GDL and bipolar plates will all
experience expansion and contraction. Because of the different
thermal expansion and swelling coefficients between these
materials, hygro-thermal stresses are introduced into the unit
cell during operation. In addition, the non-uniform current and
reactant flow distributions in the cell result in non-uniform
temperature and moisture content of the cell which could in
turn, potentially causing localized increases in the stress
magnitudes, and this leads to mechanical damage, which can
appear as through-the-thickness flaws or pinholes in the
membrane, or delaminating between the polymer membrane and gas
diffusion layers. In this work, the effects of ambient
conditions (ambient temperature and relative humidity) on the
temperature distribution, displacement, deformation, and
stresses inside a planar PEM fuel cell has been studied and
investigated. The results showed that the ambient conditions
(ambient temperature and relative humidity) have a strong impact
on the temperature distribution and hygro-thermal stresses
inside the cell.
[Full Text (PDF)] |
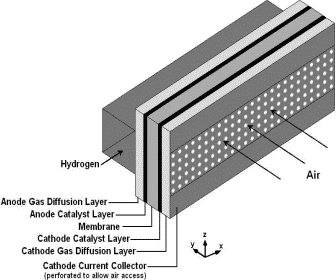 |
6.
Optimal Design of PEM Fuel Cells to Generate Maximum Power |
Optimization
study of a PEM fuel cell performance has been performed. The
study quantifies and analyses the impact of operating, design,
and material parameters on fuel cell performance and get an
optimal design for PEM fuel cells to generate maximum power. To
generate maximum power, the results show that the cell must be
operate at higher cell operating temperature, higher cell
operating pressure, higher stoichiometric flow ratio, and must
have higher GDL porosity, higher GDL thermal conductivity,
narrower gases channels, and thinner membrane. At these optimum
conditions, the result shows that the total displacement and the
degree of the deformation inside the MEA were decreased.
However, the Miss stress in the membrane was increased due to
higher cell operating temperature.
[Full Text (PDF)] |
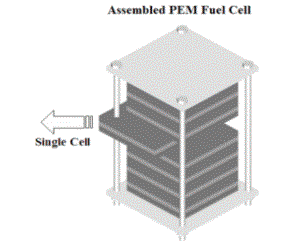 |
7.
Novel Design of a Disk-Shaped Compacted Micro-Structured
Air-Breathing PEM Fuel Cell |
The presence
of microelectromechanical system (MEMS) technology makes it
possible to manufacture the miniaturized fuel cell systems for
application in portable electronic devices. The majority of
research on micro-scale fuel cells is aimed at micro-power
applications. There are many new miniaturized applications which
can only be realized if a higher energy density power source is
available compared to button cells and other small batteries. In
small-scale applications, the fuel cell should be exceptionally
small and have highest energy density. One way to achieve these
requirements is to reduce the thickness of the cell
(compacted-design) for increasing the volumetric power density
of a fuel cell power supply. A novel disk-shaped air-breathing
micro-structured PEM fuel cell which work in still or slowly
moving air has been developed. The novel geometry enables
optimum air access to the cathode without the need for pumps,
fans or similar devices. In addition, the new design can achieve
much higher active area to volume ratios, and hence higher
volumetric power densities.
[Full Text (PDF)] |
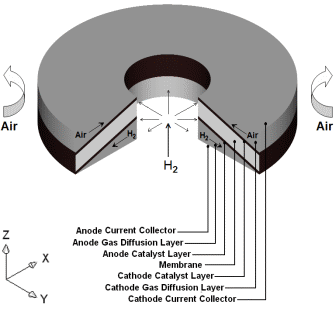 |
8.
Prediction of
Deformation and Hygro-Thermal Stresses Distribution in PEM Fuel
Cell Vehicle |
Durability
is one of the most critical remaining issues impeding successful
commercialization of broad PEM fuel cell transportation energy
applications. Automotive fuel cells are likely to operate with
neat hydrogen under load-following or load-levelled modes and be
expected to withstand variations in environmental conditions,
particularly in the context of temperature and atmospheric
composition. In addition, they are also required to survive over
the course of their expected operational lifetimes i.e., around
5,500 hrs, while undergoing as many as 30,000 startup/shutdown
cycles. The damage mechanisms in a PEM fuel cell are accelerated
by mechanical stresses arising during fuel cell assembly (bolt
assembling), and the stresses arise during fuel cell running,
because it consists of the materials with different thermal
expansion and swelling coefficients. Therefore, in order to
acquire a complete understanding of the damage mechanisms in the
membrane, mechanical response under steady-state hygro-thermal
stresses should be studied under real cell operating conditions
and in real cell geometry (three-dimensional). In this work,
full three-dimensional, non-isothermal computational fluid
dynamics model of a PEM fuel cell has been developed to simulate
the stresses inside the PEM fuel cell, which are occurring
during fuel cell assembly (bolt assembling), and the stresses
arise during fuel cell running due to the changes of temperature
and relative humidity.
[Full Text (PDF)] |
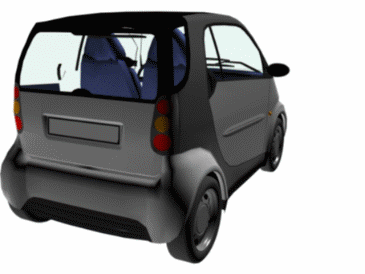 |
9.
Analysis of Transport Phenomena and Electrochemical Reactions in
a Tubular-Shaped PEM Fuel Cell |
A fuel cell
is most interesting new power source because it solves not only
the environment problem but also natural resource exhaustion
problem. CFD modeling and simulation for heat and mass transport
in PEM fuel cells are being used extensively in researches and
industrial applications to gain better understanding of the
fundamental processes and to optimize fuel cell designs before
building a prototype for engineering application. In this
research, full three-dimensional, non-isothermal computational
fluid dynamics model of a tubular-shaped proton exchange
membrane (PEM) fuel cell has been developed. This comprehensive
model accounts for the major transport phenomena such as
convective and diffusive heat and mass transfer, electrode
kinetics, transport and phase-change mechanism of water, and
potential fields in a tubular-shaped PEM fuel cell. The model
explains many interacting, complex electrochemical, and
transport phenomena that cannot be studied experimentally.
Three-dimensional results of the species profiles, temperature
distribution, potential distribution, and local current density
distribution are presented and analysed, with the focus on the
physical insight and fundamental understanding.
[Full Text (PDF)] |
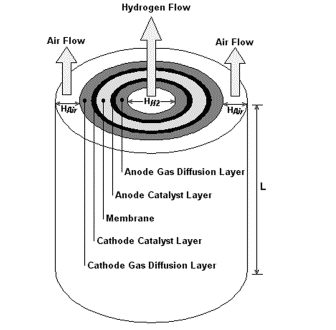 |
10.
Performance
Optimization of a PEM Hydrogen-Oxygen Fuel Cell |
The
objective was to develop a semi-empirical model that would
simulate the performance of proton exchange membrane (PEM) fuel
cells without extensive calculations. A fuel cell mathematical
module has been designed and constructed to determine the
performance of a PEM fuel cell. The influence of some operating
parameters on the performance of PEM fuel cell has been
investigated using pure hydrogen on the anode side and oxygen on
the cathode side. The present model can be used to investigate
the influence of process variables for design optimization of
fuel cells, stacks, and complete fuel cell power system. The
possible mechanisms of the parameter effects and their
interrelationships are discussed. In order to assess the
validity of the developed model a real PEM fuel cell system has
been used to generate experimental data. The comparison shows
good agreements between the modelling results and the
experimental data. The model is shown a very useful for
estimating the performance of PEM fuel cell stacks and
optimization of fuel cell system integration and operation.
[Full Text (PDF)] |
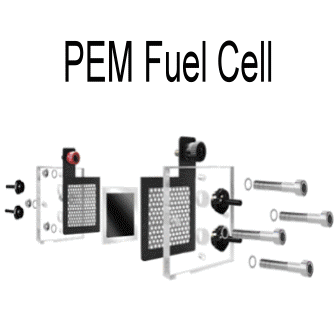 |
11.
Analysis of Transport Phenomena and Electrochemical Reactions in
a Micro PEM Fuel Cell |
Micro-fuel
cells are considered as promising electrochemical power sources
in portable electronic devices. The presence of
microelectromechanical system (MEMS) technology makes it
possible to manufacture the miniaturized fuel cell systems. The
majority of research on micro-scale fuel cells is aimed at
micro-power applications. Performance of micro-fuel cells are
closely related to many factors, such as designs and operating
conditions. CFD modeling and simulation for heat and mass
transport in micro PEM fuel cells are being used extensively in
researches and industrial applications to gain better
understanding of the fundamental processes and to optimize the
micro fuel cell designs before building a prototype for
engineering application. In this research, full
three-dimensional, non-isothermal computational fluid dynamics
model of a micro proton exchange membrane (PEM) fuel cell has
been developed. This comprehensive model accounts for the major
transport phenomena such as convective and diffusive heat and
mass transfer, electrode kinetics, transport and phase-change
mechanism of water, and potential fields in a micro PEM fuel
cell. The model explains many interacting, complex
electrochemical, and transport phenomena that cannot be studied
experimentally. Three-dimensional results of the species
profiles, temperature distribution, potential distribution, and
local current density distribution are presented and analysed,
with the focus on the physical insight and fundamental
understanding.
[Full Text (PDF)] |
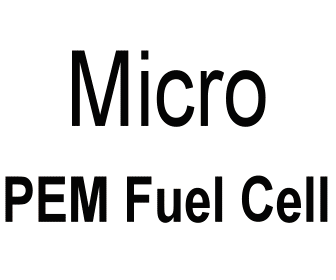 |
12.
Analysis of Transport Phenomena and Electrochemical Reactions in
a Micro PEM Fuel Cell with Serpentine Gas Flow Channels |
Micro-fuel
cells are considered as promising electrochemical power sources
in portable electronic devices. The presence of
microelectromechanical system (MEMS) technology makes it
possible to manufacture the miniaturized fuel cell systems. The
majority of research on micro-scale fuel cells is aimed at
micro-power applications. Performance of micro-fuel cells are
closely related to many factors, such as designs and operating
conditions. CFD modeling and simulation for heat and mass
transport in micro PEM fuel cells are being used extensively in
researches and industrial applications to gain better
understanding of the fundamental processes and to optimize the
micro fuel cell designs before building a prototype for
engineering application. In this research, full
three-dimensional, non-isothermal computational fluid dynamics
model of a micro proton exchange membrane (PEM) fuel cell with
serpentine gas flow channels has been developed. This
comprehensive model accounts for the major transport phenomena
such as convective and diffusive heat and mass transfer,
electrode kinetics, transport and phase-change mechanism of
water, and potential fields in a micro PEM fuel cell. The model
explains many interacting, complex electrochemical, and
transport phenomena that cannot be studied experimentally.
[Full Text (PDF)] |
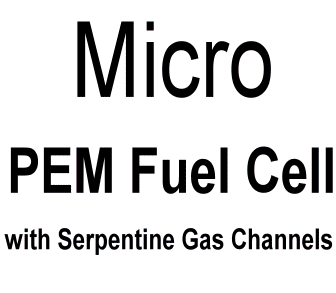 |
13.
Analysis of Transport Phenomena and Electrochemical Reactions in
a Micro PEM Fuel Cell with Nature Inspired Flow Field Design |
Micro-fuel
cells are considered as promising electrochemical power sources
in portable electronic devices. The presence of
microelectromechanical system (MEMS) technology makes it
possible to manufacture the miniaturized fuel cell systems. The
majority of research on micro-scale fuel cells is aimed at
micro-power applications. Performance of micro-fuel cells are
closely related to many factors, such as designs and operating
conditions. CFD modeling and simulation for heat and mass
transport in micro PEM fuel cells are being used extensively in
researches and industrial applications to gain better
understanding of the fundamental processes and to optimize the
micro fuel cell designs before building a prototype for
engineering application. In this research, full
three-dimensional, non-isothermal computational fluid dynamics
model of a micro proton exchange membrane (PEM) fuel cell with
nature inspired flow field designs has been developed. The
design inspired from the existed biological fluid flow patterns
in the leaf. This
comprehensive model accounts for the major transport phenomena
such as convective and diffusive heat and mass transfer,
electrode kinetics, transport and phase-change mechanism of
water, and potential fields in a micro PEM fuel cell. The model
explains many interacting, complex electrochemical, and
transport phenomena that cannot be studied experimentally.
[Full Text (PDF)] |
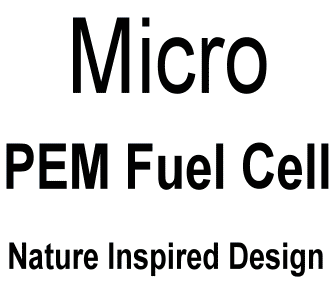 |
14.
Mechanical Behaviour of Membrane Electrode Assembly (MEA) During
Cold Start of PEM Fuel Cell from Subzero Environment Temperature |
Durability
is one of the most critical remaining issues impeding successful
commercialization of broad PEM fuel cell transportation energy
applications. Automotive fuel cells are likely to operate with
neat hydrogen under load-following or load-levelled modes and be
expected to withstand variations in environmental conditions,
particularly in the context of temperature and atmospheric
composition. In addition, they are also required to survive over
the course of their expected operational lifetimes i.e., around
5,500 hrs, while undergoing as many as 30,000 startup/shutdown
cycles.
Cold start capability and survivability of proton exchange
membrane fuel cells (PEM) in a subzero environment temperature
remain a challenge for automotive applications. A key component
of increasing the durability of PEM fuel cells is studying the
behaviour of the membrane electrode assembly (MEA) at the heart
of the fuel cell. The present work investigates how the
mechanical behaviour of MEA are influenced during cold start of
the PEM fuel cell from subzero environment temperatures.
[Full Text (PDF)] |
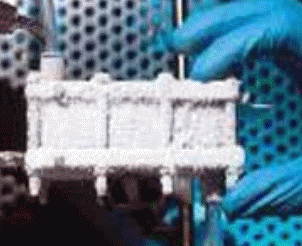 |
15.
A Parametric Study of the Natural Vibration and Mode Shapes of
PEM Fuel Cell Stacks |
A PEM fuel
cell stack is laminated with a number of plate-type cells, and
the latest model is assembled by compression from both ends of
plates. PEM fuel cells are exposed to high magnitude vibrations,
shocks, and cyclic loads in many applications. Vibrations during
operation show significant impact in the longer run of the fuel
cells. Frequencies which are not close to the resonant
frequencies or natural frequencies show very little effect on
the overall performance. However, if the frequency ranges of
operation approaches the resonant frequency range, the
probability of component failure increases. It is possible that
there will be lateral transition of cells or leakage of fuel gas
and coolant water. Therefore, it is necessary to evaluate the
effects vibration has on the fuel cell.
This work aims to understand the vibration characteristics of a
PEM fuel cell stack and to evaluate their seismic resistance
under a vibration environment. Natural frequencies and mode
shapes of the PEM fuel cell stack are modelling using finite
element methods (FEM). A parametric study is conducted to
investigate how the natural frequency varies as a function of
thickness, Young’s modulus, and density for each component
layer. In addition, this work provides insight into how the
natural frequencies of the PEM fuel cell stack should be tuned
to avoid high amplitude vibrations by modifying the material and
geometric properties of individual components. The mode shapes
of the PEM fuel cell stack provide insight into the maximum
displacement exhibited under vibration conditions that should be
considered for transportation and stationary applications.
[Full Text (PDF)] |
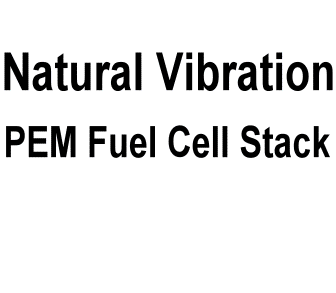 |
16.
A Parametric Study of Assembly Pressure, Thermal Expansion, and
Membrane Swelling in PEM Fuel Cells |
Proton
Exchange membrane (PEM) fuel cells are still undergoing intense
development, and the combination of new and optimized materials,
improved product development, novel architectures, more
efficient transport processes, and design optimization and
integration are expected to lead to major gains in performance,
efficiency, durability, reliability, manufacturability and
cost-effectiveness. PEM fuel cell assembly pressure is known to
cause large strains in the cell components. All components
compression occurs during the assembly process of the cell, but
also during fuel cell operation due to membrane swelling when
absorbs water and cell materials expansion due to heat
generating in catalyst layers. Additionally, the repetitive
channel-rib pattern of the bipolar plates results in a highly
inhomogeneous compressive load, so that while large strains are
produced under the rib, the region under the channels remains
approximately at its initial uncompressed state. This leads to
significant spatial variations in GDL thickness and porosity
distributions, as well as in electrical and thermal bulk
conductivities and contact resistances (both at the ribe-GDL and
membrane-GDL interfaces). These changes affect the rates of
mass, charge, and heat transport through the GDL, thus impacting
fuel cell performance and lifetime. In this paper, computational
fluid dynamics (CFD) model of a PEM fuel cell has been developed
to simulate the pressure distribution inside the cell, which are
occurring during fuel cell assembly (bolt assembling), and
membrane swelling and cell materials expansion during fuel cell
running due to the changes of temperature and relative humidity.
The PEM fuel cell model simulated includes the following
components; two bi-polar plates, two GDLs, and, an MEA (membrane
plus two CLs). This model is used to study and analyses the
effect of assembling and operating parameters on the mechanical
behaviour of PEM. The analysis helped identifying critical
parameters and shed insight into the physical mechanisms leading
to a fuel cell durability under various operating conditions.
The model is shown to be able to understand the effect of
pressure distribution inside the cell on the performance and
durability that have limited experimental data.
[Full Text (PDF)] |
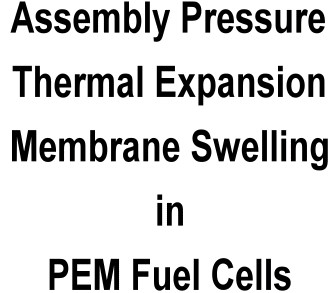 |
17.
Proton Exchange Membrane Fuel
Cells Modeling: A Review of the Last Ten Years Results of the
Fuel Cell Research Center-IEEF |
Fuel cell
technology is expected to play an important role in meeting the
growing demand for distributed power generation. In an ongoing
effort to meet increasing energy demand and to preserve the
global environment, the development of energy systems with
readily available fuels, high efficiency and minimal
environmental impact is urgently required. A fuel cell system is
expected to meet such demands because it is a chemical power
generation device, which converts the chemical energy of a
renewable clean fuel (e.g. Hydrogen) directly into electrical
energy. Still a maturing technology, fuel cell technology has
already indicated its advantages, such as its high-energy
conversion efficiency, modular design and very low environmental
intrusion, over conventional power generation equipment. Among
all kinds of fuel cells, proton exchange membrane (PEM) fuel
cells have many superior advantages. These advantages have
sparked development efforts in various quarters of industry to
open up new field of applications for PEM fuel cells. Three key
issues limiting the widespread commercialization of the PEM fuel
cells technology which are better performance, lower cost, and
long cell life. The strategy of the Fuel Cell Research Center at
the International Energy and Environment Foundation (IEEF) is to
develop the PEM fuel cells to improve their lifetime with a much
higher power density and lower cost. An overview of innovations
in this field is presented using the published results of the
center over the last decade. These innovative improvements will
show a new scenario for the future fuel cell market of the next
years.
[Full Text (PDF)] |
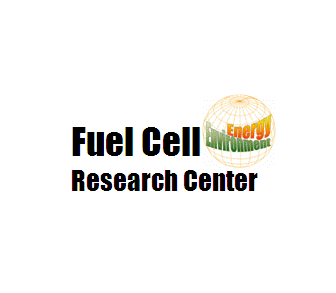 |
18.
Effect of Channel Geometrical
Configuration on the Pressure Distribution and Stress Failure in
a Running PEM Fuel Cell |
Proton
Exchange membrane (PEM) fuel cells are still undergoing intense
development, and the combination of new and optimized materials,
improved product development, novel architectures, more
efficient transport processes, and design optimization and
integration are expected to lead to major gains in performance,
efficiency, durability, reliability, manufacturability and
cost-effectiveness. PEM fuel cell assembly pressure is known to
cause large strains in the cell components. All components
compression occurs during the assembly process of the cell, but
also during fuel cell operation due to membrane swelling when
absorbs water and cell materials expansion due to heat
generating in catalyst layers. Additionally, the repetitive
channel-rib pattern of the bipolar plates results in a highly
inhomogeneous compressive load, so that while large strains are
produced under the rib, the region under the channels remains
approximately at its initial uncompressed state. This leads to
significant spatial variations in GDL thickness and porosity
distributions, as well as in electrical and thermal bulk
conductivities and contact resistances (both at the ribe-GDL and
membrane-GDL interfaces). These changes affect the rates of
mass, charge, and heat transport through the GDL, thus impacting
fuel cell performance and lifetime. In this study, computational
fluid dynamics (CFD) model of a PEM fuel cell has been developed
to simulate the pressure distribution inside the cell, which are
occurring during fuel cell assembly (bolt assembling), and
membrane swelling and cell materials expansion during fuel cell
running due to the changes of temperature and relative humidity.
The PEM fuel cell model simulated includes the following
components; two bi-polar plates, two GDLs, and, an MEA (membrane
plus two CLs). This model is used to study and analyse the
effect of channel geometrical configuration on the mechanical
behaviour of the PEM fuel cell components. The analysis helped
identifying critical parameters and shed insight into the
physical mechanisms leading to a fuel cell durability under
various conditions. The model is shown to be able to understand
the effect of pressure distribution inside the cell on the
performance and durability that have limited experimental data.
[Full Text (PDF)] |
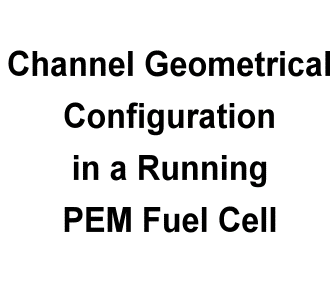 |
19.
Three-dimensional solid mechanics-CFD modeling of a PEM fuel
cell stack |
PEM fuel
cell stack assembly process, including clamping pressure,
material properties of each component, design
(component thickness and cell active area), and number of cells
in the stack are important factors influencing the performance
and durability of the PEM fuel cell stack. Furthermore, when
temperature and relative humidity increase during operation, the
membrane absorbs water and swells. Since the relative position
between the top and bottom end plates is fixed, the polymer
membrane is spatially confined. Thus the GDL will be further
compressed under the land and the intrusion into channel becomes
more significant. Assembly pressure, contact resistance,
membrane swelling and operating conditions, etc., combine to
yield an optimum assembly pressure. The clamping pressure is
therefore a critical parameter for optimal fuel cell performance
and durability. Too high, too low, or inhomogeneous compressions
have negative effects on the performance and durability of the
stack. In this study, full three-dimensional, non-isothermal
computational fluid dynamics (CFD) detailed model of a PEM fuel
cell stack has been developed and coupled with a solid mechanics
model to simulate the stress distribution inside the stack,
which are occurring during fuel cell assembly (bolt assembling),
and membrane swelling and cell materials expansion during fuel
cell running due to the changes of temperature and relative
humidity. The PEM fuel cell stack model simulated includes the
following all components in full details; two end-plates, two
current plates, two bi-polar plates with straight flow channels
for reactants and cooling serpentine water flow channel on the
upper face of cathode bi-polar plate, two GDLs, two gaskets,
and, an MEA (membrane plus two CLs). The model is shown to be
able to understand the many interacting, complex
electrochemical, transport phenomena, with stress distribution
inside the stack during operation on the performance and
durability of the stack that have limited experimental data.
Furthermore, the model is shown to be able to provide a
computer-aided tool for design and optimize future fuel cell
stack with much higher power density, long stack life, and lower
cost.
[Full Text (PDF)] |
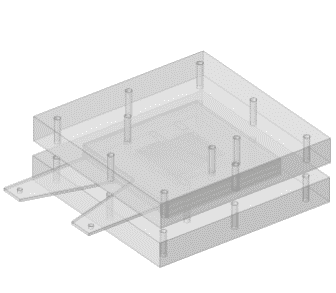 |
20.
Influence of the number of cells on the stress distribution in a
running PEM fuel cell stack |
Mechanical
degradation is often studied in single-cell proton exchange
membrane (PEM) fuel cell stack models in assembly process. This
however, can increase substantially when moving from assembly
process to operation conditions; and also from single-cell to
multiple cells. In this study, PEM fuel cell stacks consisting
of 1, 3, and 5 cells with an active area of 25 cm2 per cell have
been simulated in operation mode. Three dimensional
non-isothermal solid mechanics-CFD model of a PEM fuel cell
stack, integrating the real full scale geometry of all
components have been used to study the influence of the number
of cells on the stress distribution in a running PEM fuel cell
stack. Simulation of a running multi cells stack was successful
and has not been previously seen in literatures work. The
results showed that the center of the electrode tends to
un-displacement. This un-displacement area increases by
increasing the clamping torque. The deformations in the stack
components during operation were about ten times higher than
during assembly process. During assembly process, the increasing
in the number of cells increases the total displacement
distribution. These status were different during operation, the
increasing in the number of cells enhances the uniformity of the
total displacement. Increasing the number of cells enhances the
uniformity of the mechanical state. The better contact pressure
homogeneity was obtained with the greater number of cells and
leads to the lower contact resistance. In general, the results
showed lower stresses values with lower distributions and more
homogeneous and uniformity in the stack that consisting of multi
cells.
[Full Text (PDF)] |
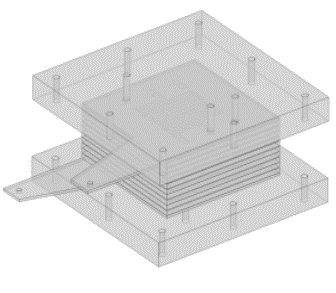 |
|